Viele Instandhalter wissen, dass Planung und Struktur zur Verbesserung der Instandhaltung beitragen. Weniger haben allerdings eine vollständige Übersicht - oder es fehlen die digitalen Werkzeuge, die notwendig sind, um den richtigen Überblick über die Instandhaltung zu bekommen.
Internationale Instandhaltungsstandards wie EN-13306 stellen sicher, dass alle Beteiligten gleich arbeiten und dass Sie über eine zuverlässige Dokumentation und Daten zur Analyse verfügen. Die Konzepte sind replizierbar und funktionieren international, so dass Sie schneller skalieren können.
Doch welche Auswirkungen kann die Umsetzung einer solchen Instandhaltungsnorm haben?
Dieser Anwendungsfall zeigt den Weg vom Chaos zur Struktur bei einem bekannten Lebensmittelproduzenten. Hier sehen Sie, was das Unternehmen durch die Strukturierung der Arbeit nach Instandhaltungsstandards und die Implementierung einer neuen Instandhaltungssoftware erreicht hat.
"Repariere es, wenn es kaputt ist"
Im Jahr 2010 gründete ein Lebensmittel- und Getränkehersteller eine neue Instandhaltungsorganisation mit 36 Technikern und Managern, von denen die Hälfte neu eingestellt wurde. Die alten Instandhaltungsabteilungen des Unternehmens nutzten Maximo CMMS von IBM, aufgeteilt in elektrische und mechanische Instandhaltungsgruppen.
Außerdem gab es eine Aufteilung der Wartungsgruppen auf verschiedene Produktionsabschnitte, was zu einer starken Suboptimierung der Instandhaltungsressourcen führte.
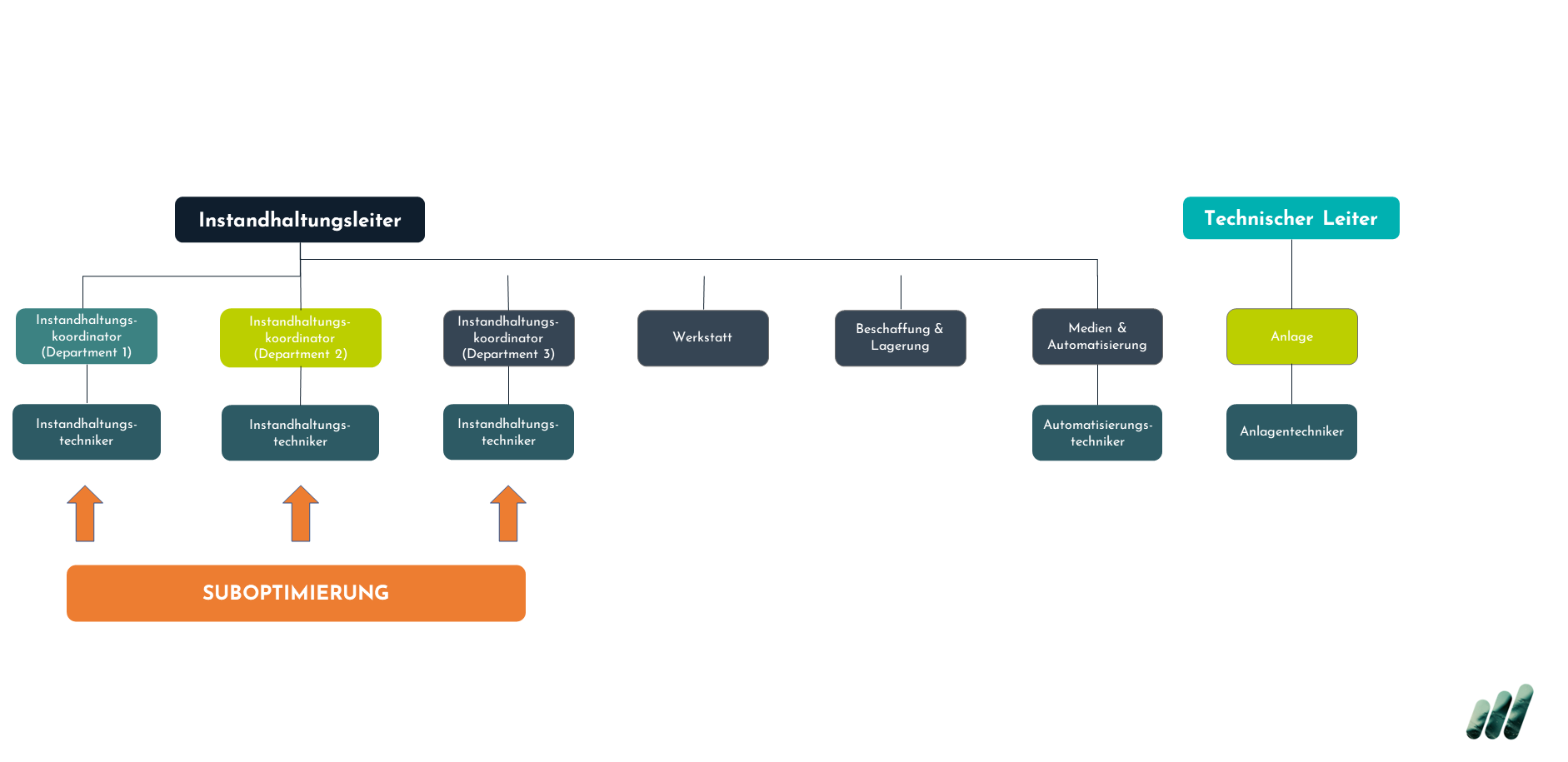
Mehr als 60 % der gemeldeten Zeit entfielen auf die korrigierende Instandhaltung. Mit anderen Worten: Das Unternehmen führte die Wartung meist erst nach einem Maschinenausfall durch, was zu Problemen bei der Planung von vorbeugenden und verbessernden Instandhaltungsmaßnahmen führte.
Das Budget für alle Instandhaltungsaktivitäten wurde von der Produktion verwaltet und kontrolliert. Das bedeutete, dass sie die Prioritäten für die Instandhaltungsaktivitäten anders setzen konnte. Zudem führte es dazu, dass sie andere Maßnahmen, die nicht mit der Wartung zusammenhingen, als Wartungsarbeiten ausgeben konnte.
Außerdem gab es zwei Gruppen, eine elektrische und eine mechanische, die außerhalb der normalen Arbeitszeiten Bereitschaftsdienst hatten. Die sechs Techniker in jeder Gruppe erhielten etwa 60 Anrufe pro Monat.
Die Arbeitsabläufe waren stressig. Infolgedessen herrschte eine schlechte Stimmung, die dazu führte, dass hinter dem Rücken der anderen geredet wurde - intern in der Instandhaltungsorganisation und zwischen Produktion und Instandhaltung.
Umgestaltung einer Instandhaltungsorganisation
Unser Team begann mit der Implementierung der Instandhaltungssoftware (CMMS) von MaintMaster, einschließlich Schulungen für 230 Mitarbeiter in der Produktion. Außerdem wurde eine neue Instandhaltungsorganisation auf der Grundlage der neuesten Norm EN-13306 eingeführt. Um sicherzustellen, dass jeder Mitarbeiter den Instandhaltungsstandard verstand und befolgte, wurde zusätlich das gesamte Instandhaltungspersonal in der Norm geschult.
Zur weiteren Unterstützung wurde ein Instandhaltungshandbuch eingeführt und das Auftragsmanagement in MaintMaster mit Kategorien und Codes gemäß der Norm EN-13306 eingeführt.
Auf struktureller Ebene bestand eine große Veränderung darin, dass die Verantwortung für das Budget auf die Instandhaltungsorganisation übertragen wurde - mit Instandhaltungsabteilungen, die an den Standard angepasst wurden.
Eine weitere wichtige Entscheidung war die Änderung der Arbeitsmethoden für die geplanten Aktivitäten, so dass nicht mehr wie früher große Mengen an Aufträgen für die Sommer- und Weihnachtspause geplant wurden. Stattdessen begann man mit der Planung von Wartungsaktivitäten für wiederkehrende Stillstände während des ganzen Jahres.
Die Wende zum Besseren
Die Instandhaltungssoftware von MaintMaster trug auch zur Einführung eines neuen Konzepts mit neuen Rollen für Techniker mit Verantwortung von Produktionslinien bei. Die neue Rolle hieß "Techniker mit Vorbereitungsverantwortung", welche mehr Befugnisse und mehr Eigenverantwortung vorsah. Außerdem verbesserte das Team das Ersatzteilmanagement und schloss eine Vereinbarung mit einem wichtigen Lieferanten für Standard-Ersatzteile ab.
Mit der neuen Instandhaltungssoftware, den Schulungen zu den Instandhaltungsstandards sowie dem Instandhaltungshandbuch, begann der Lebensmittelproduzent, sich auf das Wesentliche zu konzentrieren. Eine direkte Reaktion darauf war die Auslagerung einfacher Aufgaben, um sich auf Schlüsselkompetenzen zu konzentrieren.
Die neuen Standards und Möglichkeiten zur Verwaltung wiederkehrender vorbeugender Wartungsaufgaben in MaintMaster brachten das Unternehmen auf die Überholspur, um Struktur und Kontrolle zu erlangen. Die Implementierung von geplanten, häufigen 8-stündigen Wartungsstopps für die kritischen Maschinen, half sicherzustellen, dass es keine Überraschungen gab, die den Betrieb aufhielten.
Und so sah die neue Struktur aus, welche MaintMaster in das Unternehmen einführte:
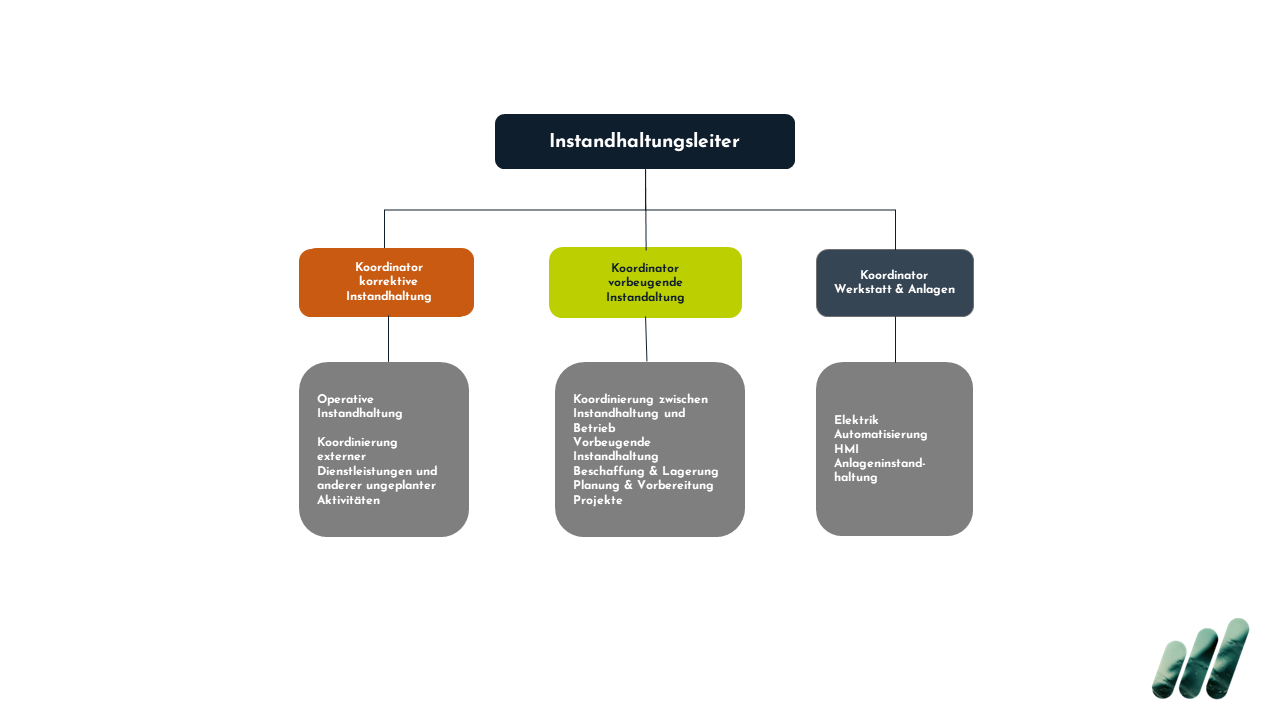
Eine bemerkenswerte strukturelle Veränderung war die Verringerung der Zahl der Verantwortlichkeiten. Mit einer gezielteren und zielgerichteteren Instandhaltungsorganisation begann das Unternehmen wie eine gut geölte Maschine zu laufen.
Das Unternehmen begann, nach dem "Blue Box"-Konzept zu arbeiten, d. h. Aufträge mit Anweisungen und allen erforderlichen Ersatzteilen in blauen Boxen vorzubereiten, um die Arbeitseffizienz zu verbessern. Um einen besseren Zugang zu künftigen Talenten zu erhalten, wurde mit einer lokalen Schule zusammengearbeitet, um neue Mitarbeiter zu technischen Bedienern in der Produktion auszubilden.
Insgesamt war der Wandel enorm - und die Auswirkungen ebenso.
Die Ergebnisse
Die Tage der ungeplanten, korrektiven Instandhaltung waren fast vorbei. Innerhalb von fünf Jahren hatte der Lebensmittel- und Getränkeproduzent seine Instandhaltungsorganisation komplett verändert und neue Arbeitsabläufe eingeführt.
Nach Anwendung unserer Empfehlungen, einschließlich der Umstellung auf die Instandhaltungssoftware von MaintMaster, waren die wichtigsten Ergebnisse:
- Verringerung der sofortigen (ungeplanten) korrigierenden Wartung von 60 % auf 18 %
- Verringerung der jährlichen Instandhaltungskosten von 4,8 Millionen auf 3,5 Millionen Euro (-26 %)
- Steigerung des Produktionsvolumens von 16,5 Millionen Tonnen pro Jahr auf 22,5 Millionen (+27%)
- Verringerung der technischen Ausfallzeiten von 18 % auf 3 %
Das Wartungspersonal blieb während der Umstellung mit etwa 35 Personen gleich groß. Sie reduzierten ihre geplante Produktion von fünf Schichten mit einigen Überstunden auf drei Schichten mit Überstunden.
Aufgrund der geringeren Anzahl von Maschinenproblemen wurde die Zahl der Bereitschaftsdienste von zwei Gruppen mit 12 Technikern auf eine Gruppe mit acht Technikern reduziert. Auch die Zahl der Anrufe ging von rund 60 auf 20 pro Monat zurück.
Insgesamt war die positive Entwicklung der Atmosphäre und der Arbeitssituation großartig.
Sowohl die Instandhaltung als auch die Maschinen liefen nun reibungslos, und die Mitarbeiter spürten dies. Aber es gab immer noch neue Verbesserungsmöglichkeiten, wie die Verbesserung der Beziehung zwischen Produktion und Instandhaltung...
...aber ist das nicht immer der Fall?
Lektion gelernt
Standards sind für die Lebensmittel- und Getränkeindustrie von entscheidender Bedeutung. Angesichts der strengen Vorschriften und Kontrollen, die sicherstellen sollen, dass die Produkte unbedenklich gegessen oder getrunken werden können, kann die kleinste Abweichung zu einer Kontamination führen. Dies könnte verheerende Auswirkungen auf die Öffentlichkeit und die Wirtschaftlichkeit haben.
Die Auswirkungen einer Abweichung zu den Instandhaltungsstandards können ebenfalls weitreichend sein. Am häufigsten zeigt sich dies in einer übermäßigen Konzentration auf die korrektive Instandhaltung - ein Ansatz, der versucht zu reparieren, was bereits kaputt ist.
Eine Strategie und Planung gemäß den Instandhaltungsstandards wird sich positiv auswirken. Diese Geschichte ist nur eine von vielen, die zeigt, dass Unternehmen in der Lebensmittel- und Getränkeindustrie jährlich Millionen einsparen, das Produktionsvolumen steigern und die technischen Ausfallzeiten erheblich reduzieren können, wenn sie auf die richtigen Methoden setzen.
Gute Praktiken brauchen die richtigen Werkzeuge. Die Instandhaltungssoftware von MaintMaster ist von Instandhaltungsexperten für Instandhaltungsexperten entwickelt worden. Sie können die Instandhaltungssoftware an Ihre Bedürfnisse anpassen, den Wartungsstandard abbilden und schnell mit Best Practices beginnen.