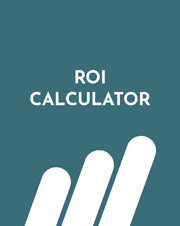
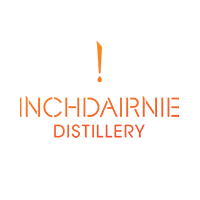
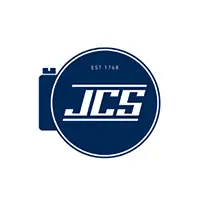
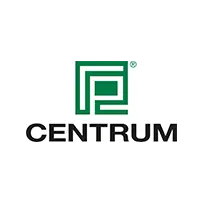
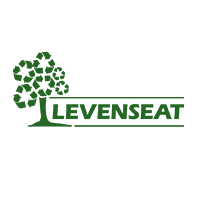
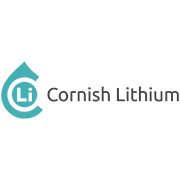
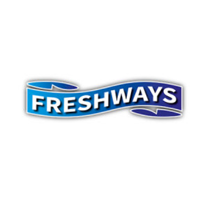
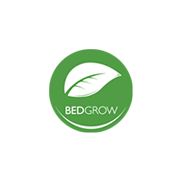
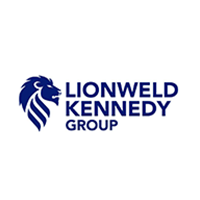
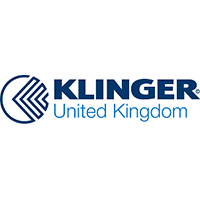
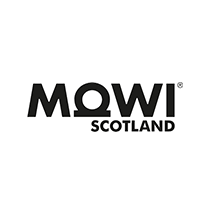
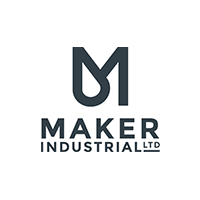
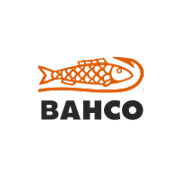
Losing control of your work is dangerous—even life-threatening. ⛔
Failing to stay on top of daily monitoring in your department can be dangerous.
As an employer, you’re responsible for ensuring that monitoring is properly carried out and documented.
Examples of critical daily inspections include moving vehicles, pressurised equipment, or proper ventilation.
It’s essential to ask the right questions and have the correct forms at hand. So, how do you tackle this challenge?
We’ve got a great idea for you 👇
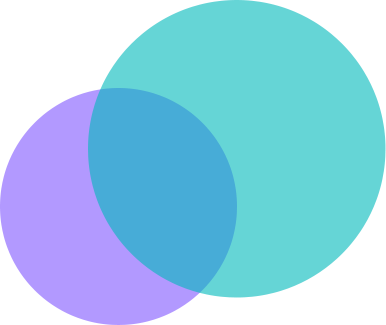
Here’s how it works in MaintMaster.
It’s really simple.
1.
One QR code, one object
Every object in MaintMaster automatically receives a QR code. During a daily inspection, simply scan the QR code to be taken directly to the form for that specific object.
No more risks.
A form tailored to your needs
Of course, different objects can have different types of forms. Just configure the form exactly as you need it.
Once the daily inspection is complete, you can easily check if anything else needs attention.
Naturally, you have full access to all inspection reports.
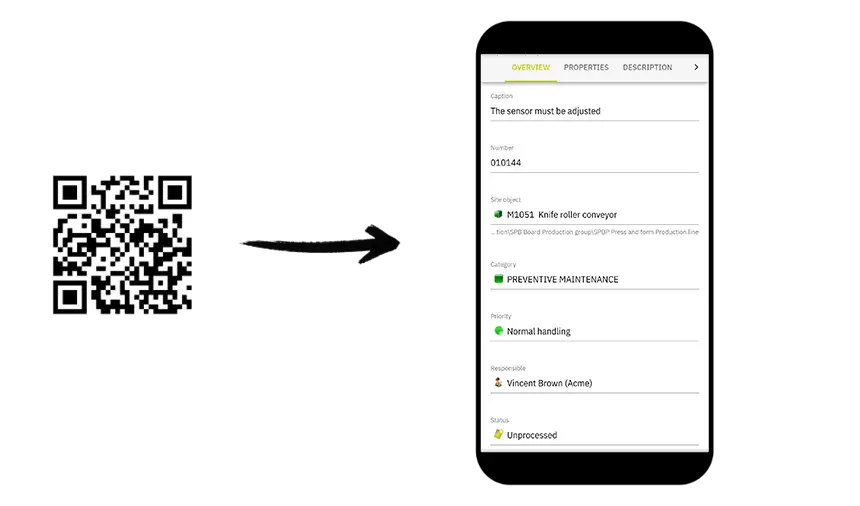
2.
Complete Control
MaintMaster provides you with a clear overview of your various inspections.
Categorise them as you see fit. Receive notifications when something is flagged or requires repair.
A technician can, of course, perform a follow-up inspection if an issue is detected—or let the system handle it automatically.
Enhanced Safety and Traceability
You can see who created what and when. And if you need the information later, it’s just one click away.
.
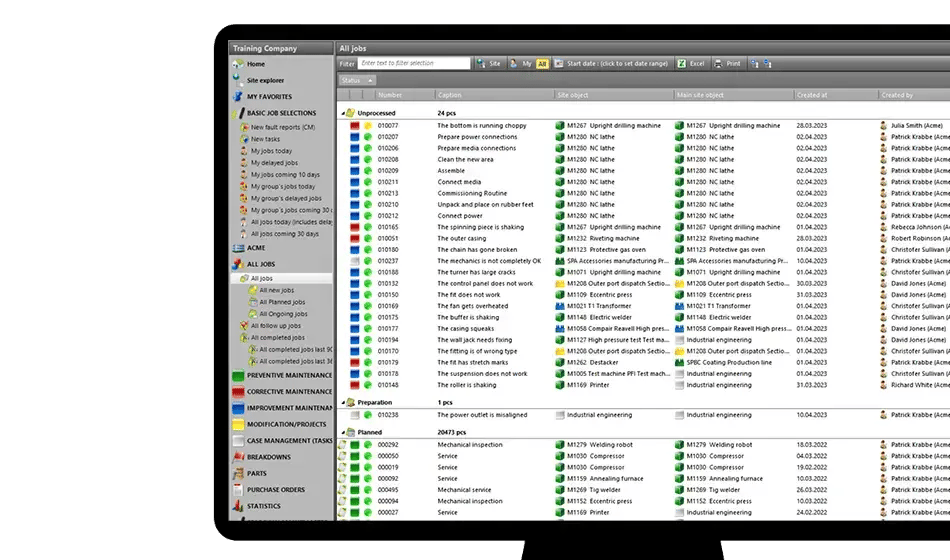
Learn More About MaintMaster
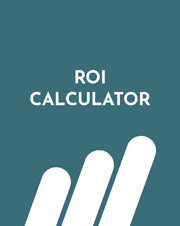
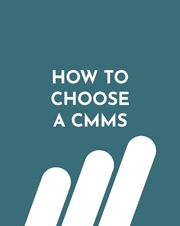
How to choose a CMMS [Guide]
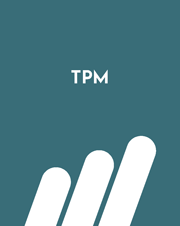
TPM (Total Productive Maintenance)
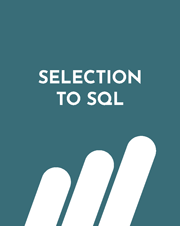
Selection to SQL in just 2 minutes
Read selected stories from our customers
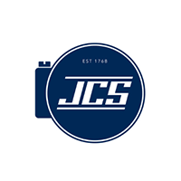
JCS Hi-Torque's Pursuit of Maintenance Excellence
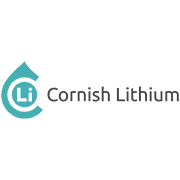
MaintMaster is perfect for Cornish Lithium's growth plans
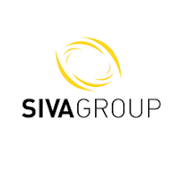
How Siva Group leveraged MaintMaster CMMS for organisational growth
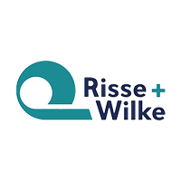
MaintMaster simplifies work at Risse + Wilke
We’d be happy to tell you more about our QR codes or how MaintMaster’s maintenance software can support you and your maintenance team.
If you're not ready for a demo yet, that's perfectly fine. Feel free to explore what else our maintenance system has to offer anytime.