What is CMMS software? Benefits, Definition, Use Cases, Guides
Table of content
KEY TAKEAWAYS
CMMS (Computerised Maintenance Management System): A CMMS is a tool designed to help organisations manage and optimise their maintenance activities. It assists maintenance teams in planning, executing, and tracking maintenance tasks.
Benefits:- Maximising assets to ensure operational safety and reliability.
- Minimising downtime through efficient maintenance planning.
- Controlling maintenance costs.
- Streamlining maintenance work processes.
- Making maintenance tasks easier for employees.
- Emphasising preventive maintenance to avoid breakdowns.
- Work Order Management: Assign tasks to technicians and track their completion.
- Scheduling Tool: Efficiently planning maintenance tasks.
- Reporting: Allowing employees to report defects for quick resolution.
- Documentation: Maintaining a comprehensive repair history for equipment.
- Planning: Using data for future maintenance decisions.
- Inventory & Spare Parts: Effectively managing spare parts inventory.
Real-World Use Cases: Real-world examples at Inchdairnie Distillery and Bedgrow demonstrate the practical benefits of using MaintMaster.
Advantages of Going Digital: Analogue maintenance processes can be error-prone and lack automation. A maintenance software helps in automating tasks, improving accuracy, and facilitating scalability as a company grows.
Cloud-Based CMMS: A Cloud-based system offers advantages of enhanced accessibility, cost-efficiency, collaboration, and security, ensuring that your system remains up-to-date.
Inventory Management: In a CMMS like MaintMaster, inventory management is precise, with cataloguing of equipment and spare parts, real-time tracking, usage history monitoring, and efficient issue and return processes.
CMMS Mobile App: A system you can access from your mobile device provides easy access to records, work order history, safety information, and work order management. This simplifies communication and enhances Mobile Maintenance.
Predictive Maintenance vs. Corrective Maintenance: Predictive Maintenance, driven by CMMS, offers numerous benefits, including minimising downtime, optimising asset longevity, reducing maintenance costs, enhancing safety, and boosting efficiency.
Maintenance Manual: The manual outlines a clear vision for achieving peak availability during planned operations and provides a comprehensive strategy and policy for achieving maintenance excellence.
Internet of Things: Incorporating IoT (Internet of Things) devices, enabling better asset performance insights, proactive maintenance, cost reduction, safety enhancement, and increased operational efficiency.
Choosing a CMMS: Selecting and implementing a system involves identifying key stakeholders, understanding their requirements, and following a process for successful implementation.
Implementing a CMMS: Implementing a CMMS requires defining your mission and vision, reviewing current maintenance processes, researching CMMS options, and training maintenance teams.
System Integration: Integrating maintenance software involves identifying assets, entering data, testing and refining the system, and training maintenance teams.
CMMS vs. EAM: CMMS is maintenance-focused, cost-effective, and customisable, making it suitable for organisations primarily concerned with maintenance management. EAM (Enterprise Asset Management) systems provide a comprehensive solution for managing various assets, processes, and analytics.
Choosing the Right System: The decision between CMMS and EAM depends on an organisation's specific needs and resources. CMMS is the ideal choice for targeted maintenance management.
Streamline Maintenance with CMMS:
A Computerised Maintenance Management System efficiently manages preventive maintenance, requiring careful planning for effectiveness. By gathering and directing tasks, it aids teams in planning and executing various maintenance activities for operational safety and reliability.
- Maximise assets
- Minimise downtime
- Control costs
- Streamline maintenance
- Simplify for employees
- Take control of Preventive Maintenance
Maintenance software gathers information and directs tasks, offering valuable assistance in planning and executing various maintenance activities for operational safety.
Work Order Management
Maintenance Managers can use a Computerised Maintenance Management System to describe tasks and receive various solutions. The CMMS will then direct the task to the appropriate technician.
Once the work is finished, the technician in charge can mark the work order as completed in the system, informing the maintenance manager that the task has been completed. This process helps to streamline maintenance work and improve the efficiency of maintenance operations.
Scheduling Tool
Effective planning is essential for the maintenance team to ensure that all necessary maintenance tasks are completed on schedule. Maintenance Management Software will help by providing a reliable work calendar and sending reminders to the person responsible for each task.
This helps the maintenance team to distribute the workload and ensures that no recurring maintenance is overlooked. By organising their planning in this way, the maintenance team can ensure that all maintenance tasks are completed efficiently and effectively.
Reporting
A maintenance system allows all employees to report on defects and makes these reports visible to everyone in the organisation. When a defect is reported, it can be assigned to the appropriate employee for correction.
The defect is also reported to the appropriate manager to ensure it is addressed promptly. This process helps to ensure that defects are identified and corrected efficiently, improving the reliability and performance of the organisation's assets.
Documentation
A maintenance system logs all repairs, providing a comprehensive history of the maintenance and repairs carried out on equipment. This is particularly useful for maintenance teams managing older equipment, as these machines may have an extensive repair history.
Having access to this information allows maintenance engineers and teams to refer to previous repairs when a problem arises, helping to ensure that future repairs are carried out correctly.
Anyone can access this information anytime, making it convenient for the maintenance team.
Planning
The maintenance software collects data that can be used to make decisions about future maintenance and investment. The system also allows data to be collected on specific parts of the operation, which can be analysed to determine how often they are serviced.
This information, together with data from previous maintenance, can be used to make informed decisions about future investments.
Inventory & Spare Parts
A CMMS helps maintenance teams effectively store and manage a large spare parts inventory. It allows teams to track the number of parts in stock, the number of parts used in repairs and when new parts need to be ordered.
This helps teams ensure they have the parts they need to complete repairs in a timely and efficient manner.
Through the use of a CMMS, maintenance departments become more successful and more efficient.
- 60 Better Maintenance Productivity
- 80 Reduced Manual Handling
- 50 Fewer Administration Hours
- 40 Reduced Breakdowns
Learn from the experts at Inchdairnie Distillery
“MaintMaster gives you a really easy to use maintenance tool without the cost and expertise required while managing other CMMS/EAM solutions. The total cost of ownership is a real win for us as you don’t need to be a SQL guru to get what you need into and out of the system. It is simple. The support has also been excellent and was certainly a factor in choosing MaintMaster.”
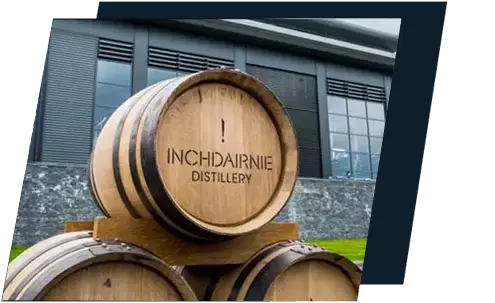
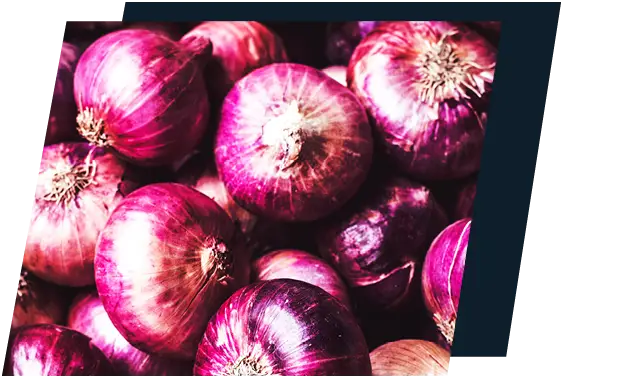
Health and safety at Bedgrow
"In health and safety, they found MaintMaster maintenance software to be an excellent tool for creating hazard reports, something they didn’t consider before. And now, with Britain outside the EU due to Brexit, they have their own certifications equivalent to the CE mark. They never thought that was possible either – but they now use MaintMaster to log all these changes."
MaintMaster S TRUSTED BY
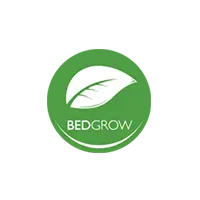
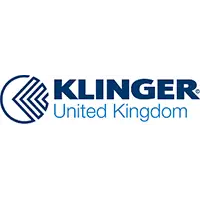
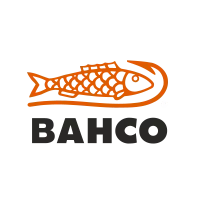
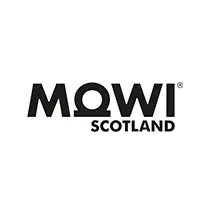
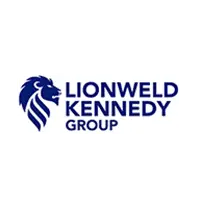
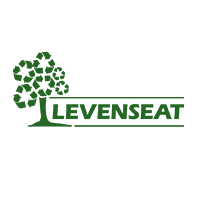
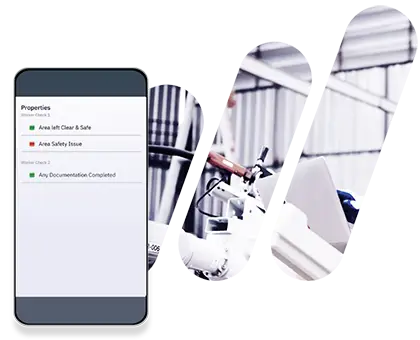
Why you should go digital
Analogue maintenance processes, relying on manual record-keeping, pose risks of errors and inconsistencies, potentially leading to confusion and delays. The lack of automated tracking in analogue methods can result in missed tasks, hindering overall efficiency.
Implementing maintenance software will address these issues by automating task tracking, providing real-time data, and enhancing efficiency. As companies grow, manual processes become challenging to scale, making an integration crucial for streamlined and accurate maintenance operations, ensuring proper system maintenance and facilitating seamless scalability.
Cloud-based software
In the evolving realm of maintenance management, choosing a cloud-based CMMS can be a transformative decision. It enhances accessibility, cost efficiency, and collaboration and ensures your system remains up to date and secure.
Ultimately, the choice between cloud-based and on-premises systems will profoundly impact your organisation's ability to adapt, grow, and thrive in an ever-changing industrial landscape.
By carefully considering your organisation's needs and priorities, you can make an informed choice that maximises efficiency and helps you stay competitive in today's challenging business environment. If you are looking to meet the requirements of tomorrow, a cloud based CMMS like MaintMaster is the way to go.
Learn more about why the cloud surpasses on-premises solutions.
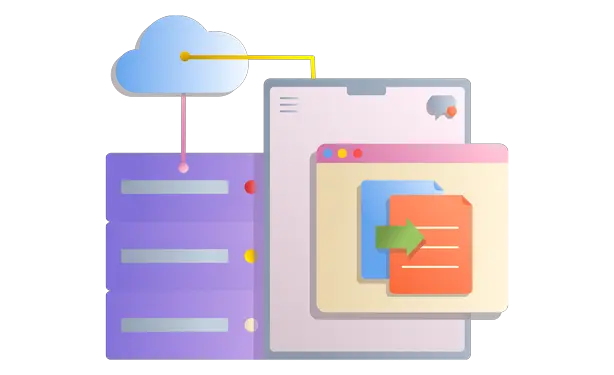
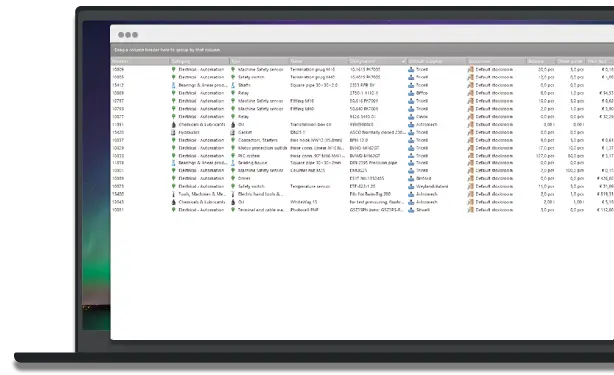
Handle inventory with a CMMS
In a system like MaintMaster, we handle inventory management with precision. We catalogue all equipment and spare parts, ensuring each item is easily identifiable. The system tracks inventory levels in real time, monitors usage history, issues and returns parts efficiently, and accesses valuable reports for strategic decision-making.
Plus, we provide timely notifications to keep you ahead in managing your inventory. In short, MaintMaster simplifies inventory management for smoother and cost-effective maintenance operations.
A system in your mobile and Tablet
The CMMS Mobile App from MaintMaster offers a user-friendly solution for effective maintenance management. With this app, you can swiftly access records, work order history, and vital data by scanning QR codes using your mobile device.
Moreover, it encompasses safety information for technicians and facilitates comprehensive work order management, all directly from your mobile device. This approach greatly streamlines communication with supervisors, marking a significant step towards achieving the pinnacle of Mobile Maintenance.
With CMMS at your fingertips, you can ensure your maintenance operations are optimally managed and effortlessly coordinated.
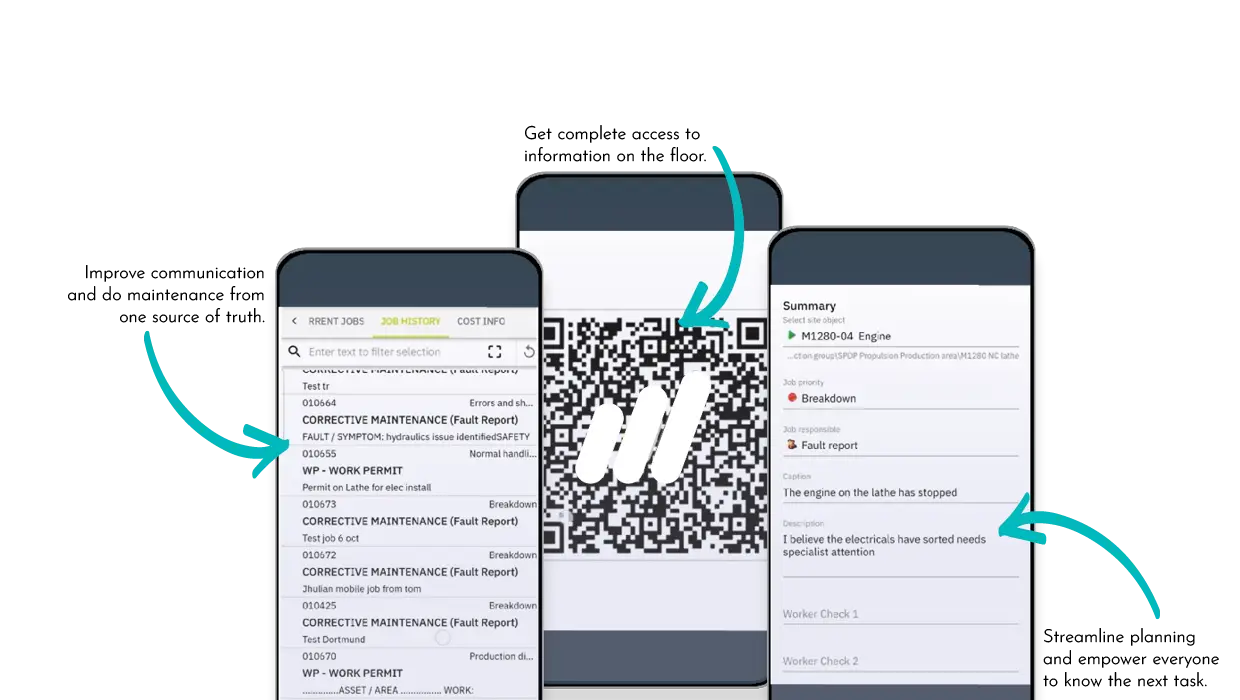
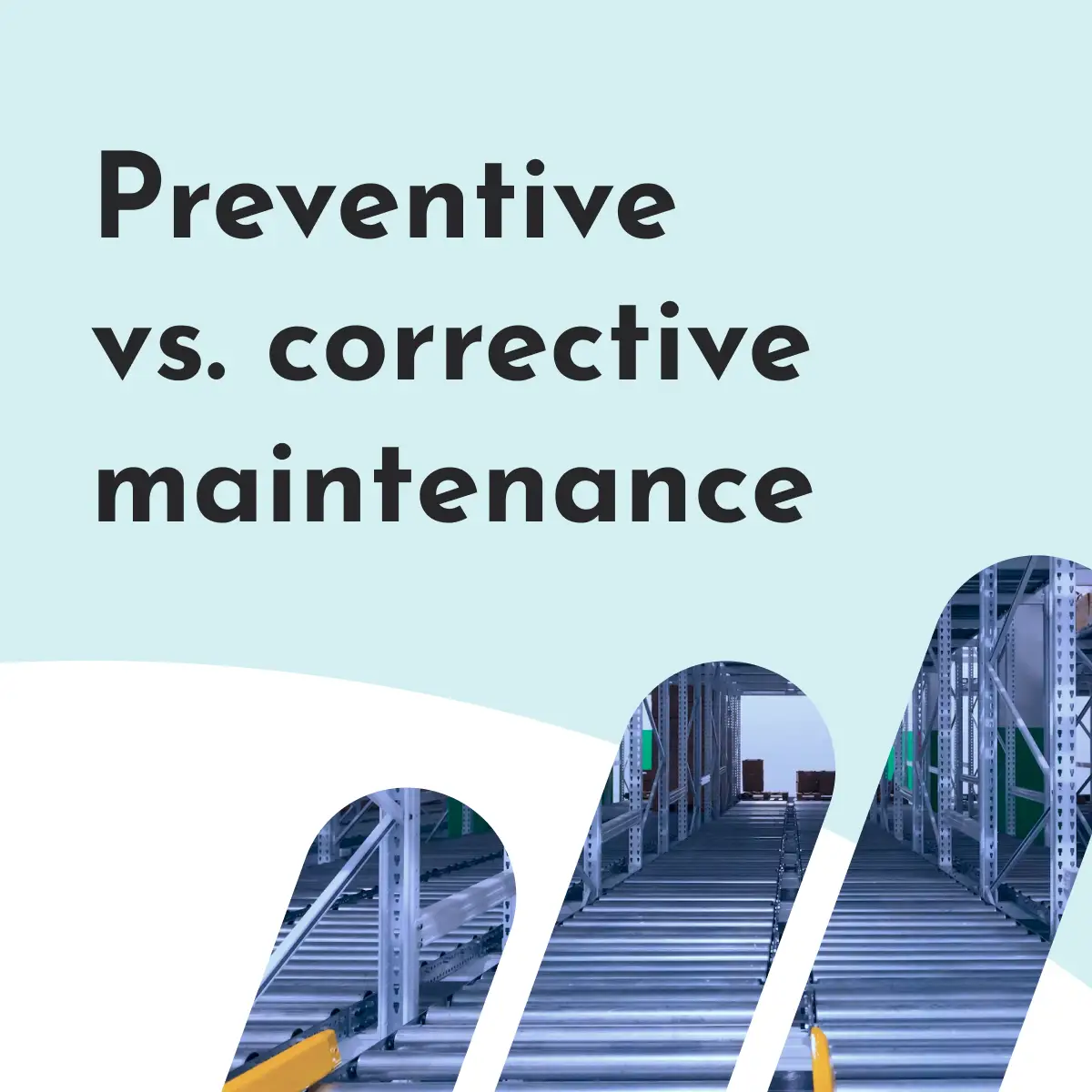
Predictive maintenance versus corrective maintenance
When considering maintenance strategies, the debate often revolves around Predictive and Corrective Maintenance.
Predictive Maintenance, guided by CMMS, signifies a significant transformation in how organisations oversee their equipment and assets. By utilising data analytics and IoT sensors, CMMS systems possess the foresight to anticipate potential equipment failures, ushering in a proactive maintenance era.
Key Benefits of Predictive Maintenance:
-
Minimise Downtime: Predict issues early, schedule maintenance during planned downtime, reducing disruptions.
-
Optimise Asset Longevity: Address problems at the start to extend equipment lifespan, reducing the need for expensive replacements.
-
Reduce Maintenance Expenditure: Avoid costly emergency repairs and optimise schedules, leading to significant cost reductions.
-
Enhance Safety: Ensure equipment operates at peak condition, reducing the risk of workplace accidents and injuries.
-
Boost Efficiency: CMMS systems provide real-time data, enabling informed decisions and more efficient resource allocation.
Learn more about Predictive VS Corrective maintenance in this expert guide
Best Practice: Standardisation
Maintenance Manual
Introducing a groundbreaking maintenance manual for maximising the performance of your machinery - a document that outlines a clear vision for attaining peak availability during planned operations.
This guide not only establishes a long-term objective for your organisation but also furnishes an extensive strategy and policy for accomplishing that objective. With this manual at your disposal, you'll be well-equipped to make informed choices and implement the required measures to guarantee your machinery operates at its peak. Prepare to elevate your business to the next level with the assistance of CMMS!
The Next Level of CMMS - What is IoT?
There are several reasons to consider incorporating the Internet of Things (IoT) into your maintenance software:
Gathering data from sensors and other IoT devices will give you better insights into your assets' performance and state. This can help you identify issues before they develop into significant problems, resulting in enhanced asset performance and decreased downtime.
By automating maintenance tasks and procedures using IoT devices and CMMS, you will save time and reduce the workforce required for asset maintenance. By detecting and addressing maintenance issues early on, you can lower repair and replacement expenses.
By utilising IoT devices to monitor the condition of your assets, you can enhance the safety and efficiency of your operations, thus reducing the risk of accidents and injuries.
Overall, integrating IoT into your CMMS-driven maintenance processes can help enhance asset performance and reliability, cut costs, and boost efficiency and safety within your operations.
How to choose a CMMS in 7 steps
As you select and implement a computerised maintenance management system for your organisation, remember that the process can take time.
This is due to the number of stakeholders that need to be involved, each with its own specific requirements and concerns. To ensure a smooth implementation, it's vital to identify these decision-makers and understand their requirements.
While every organisation is unique, we've found commonalities in the CMMS selection process.
To make it easier to follow, we've broken the process down into 7 key steps.
How do I implement a CMMS?
To implement a system, you need to define your mission and vision for what you want your maintenance department to achieve. Identify the specific improvements you hope to achieve through a CMMS - reduced maintenance costs, improved asset performance or increased efficiency.
Then, you need to review your current maintenance processes and identify areas that could be improved using the software. Once you know what you need for your asset, you must research different options and select the one that best meets your needs and budget.
Before or during the implementation phase, you will need to train your maintenance team on how to use the CMMS, including any new processes or procedures that will be introduced.
- Clearly define the mission and vision for your maintenance department.
- Identify specific improvements, such as reduced costs, improved asset performance, or increased efficiency.
Assess Current Processes:
- Review existing maintenance processes.
- Identify areas for improvement.
Research and Select:
- Research options in the market.
- Select a CMMS that aligns with your needs and budget.
Plan Implementation:
- Develop a detailed implementation plan with timelines and milestones.
- Consider phased implementation if applicable.
Team Training:
- Train the maintenance team on system usage and new procedures.
Data Migration and Testing:
- Migrate relevant data to the new CMMS.
- Conduct thorough testing, addressing any identified issues.
Rollout and Integration:
- Gradually roll out the software as per the plan.
- Ensure seamless integration with existing systems.
Continuous Improvement and Support:
- Establish a feedback loop for continuous improvement.
- Provide ongoing support to the maintenance team.
How do I integrate MaintMaster?
The first step in integrating a CMMS into a plant is to identify all the assets and equipment that will be tracked in the system. This can include machinery, plants and other assets that must be maintained.
Once the assets and equipment have been identified, the next step is to collect and enter data about each asset into the system. This may include details such as the asset's location, make and model, maintenance history and other relevant information.
Once the CMMS has been set up and users trained, it is important to test and refine the system to ensure that it meets the organisation's needs. This may include adjusting maintenance schedules, fine-tuning the data entry process, or adding additional features or capabilities to the CMMS.
A CMMS should be user-friendly
There are two main options for managing and optimising assets within an organisation: Computerised Maintenance Management Systems (CMMS) and Enterprise Asset Management (EAM) systems.
Both systems provide solutions for managing and optimising assets, each with unique advantages.
CMMS is known for its cost-effectiveness and user-friendliness. With a focused feature set and a simple user interface, these systems require less training. They are ideal for organisations with limited IT resources or those aiming for a quick maintenance management system implementation.

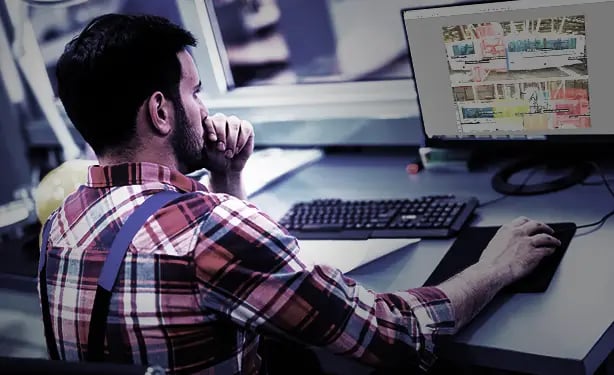
A maintenance-focused system
What differentiates CMMS from EAM systems is the specialised focus on maintenance management. A Computerised Maintenance Management System provides tools and features specifically tailored to these tasks maintenance, while EAM systems may have more general features that are less relevant.
For example, CMMS offers tools such as equipment breakdown reporting, maintenance scheduling, and inventory management, all designed to help organisations efficiently manage their maintenance processes.
For organisations with unique maintenance requirements, CMMS provides more customisation options than EAM systems. They focus on specific processes, allowing greater flexibility in workflow and data management.
This means organisations can customise the system to fit their specific needs and processes rather than trying to adapt their processes to a pre-existing system.
EAM systems might incur higher costs
Conversely, EAM systems provide a comprehensive solution, managing various assets and processes, including maintenance, inventory, procurement, and finance.
These systems often incorporate advanced analytics and reporting capabilities, aiding organisations in making well-informed decisions about their assets and processes. This is particularly advantageous for organisations needing a unified system to manage all assets, irrespective of type.
In contrast, CMMS systems typically have a more modular structure, enabling organisations to choose and implement only the necessary features—making them a cost-effective choice for those with limited budgets.
Moreover, they frequently come with pre-built integrations with other software, such as inventory management systems and accounting software, saving organisations time and effort in data integration.
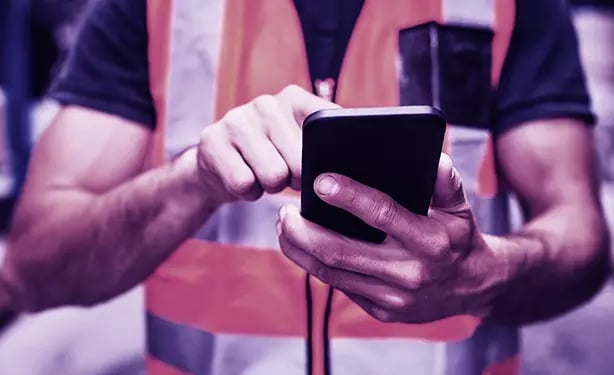
A CMMS IS THE RIGHT CHOICE FOR YOU
Whether you need a low-cost, targeted maintenance management solution or a comprehensive system to manage all your assets, CMMS and EAM systems can help. The choice between the two ultimately depends on your organisation's needs and resources.
CMMS systems (computerized maintenance management systems) are a perfect option for organisations that want to focus specifically on maintenance management but don't want to pay for expensive consultants, features, and training.
With 20+ years in Maintenance and Asset Management, Tom assists companies of all sizes in digitising operations, from SMEs to enterprises. His expertise spans diverse industries, including Facilities, Manufacturing, Environmental Services, Waste Management, Energy, and Renewables.
Tom's focus is simplifying tasks for maintenance, engineering, and safety teams through intuitive solutions and user-friendly interfaces, making them recognised contributors to business success. Join Tom to master maintenance.
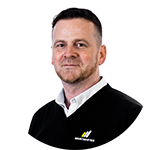
What is a CMMS?
Frequently Asked Questions
- What is Computerized Maintenance Management System?
- CMMS is a tool designed to help organizations manage and optimize maintenance activities, assisting teams in planning, executing, and tracking tasks.
- What are the benefits of using CMMS?
- Benefits include maximizing assets, minimizing downtime, controlling costs, streamlining processes, making tasks easier for employees, and emphasizing preventive maintenance.
- What are the essential components of a CMMS?
- Key components include Work Order Management, Scheduling Tool, Reporting, Documentation, Planning, and Inventory & Spare Parts.
- How does CMMS handle inventory?
- A CMMS manages inventory by cataloging equipment and spare parts, tracking in real-time, and providing efficient issue and return processes.
- Why choose CMMS over EAM?
- CMMS is user-friendly, cost-effective, and customizable for organizations primarily concerned with maintenance management.