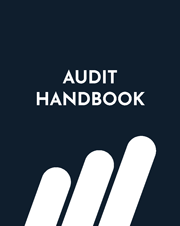
MaintMaster KPI Manual
The main reasons why KPIs are important in a maintenance department is that they allow managers to track progress towards specific goals and objectives. By setting clear, measurable targets and regularly monitoring progress, managers can ensure that the department is on track to meet its goals. This can help to drive continuous improvement, as managers can identify areas that are performing well and those that need to be addressed.
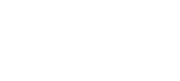
KPI - Why & When
KPIs are becoming increasingly important for managerial decision making, including in maintenance departments.
Top 3 KPI
MaintMaster can calculate KPIs in various ways. Here are the Top 3 KPIs used by our customers.
Maintenance Utilisation KPI
KPIs in maintenance can be used to measure the utilisation of resources and the overall performance of maintenance.
Breakdown Analysis KPI
Breakdown Analysis KPI measures frequency and impact of equipment failures to identify root causes & improvements.
Completion Codes KPI
Completion Codes provide maintenance managers with a clearer overview of Root Cause Analysis.
Restoration Speed KPI
Restoration Speed KPI measures how quickly equipment is returned to normal operation after a failure or breakdown.
Spare Parts KPI
Spare Parts KPI measures the efficiency of spare parts management practices in the maintenance department.
Finances KPI
KPI for finances within maintenance measures the financial performance of the maintenance function.
Learn the basic of a CMMS
Learn what a CMMS is and how it will help organizations improve the efficiency and effectiveness of their maintenance activities.
DISCOVER MORE E-BOOKS
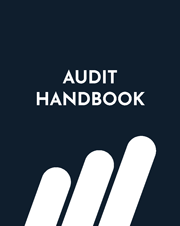
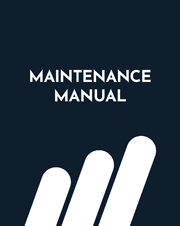