Chapter 7
KPI for spare parts
KPI for spare parts within maintenance is a measure of the effectiveness of an organisation's spare parts management practices within the maintenance function. It is an important metric for organisations that rely on equipment to meet production goals and customer demand, as efficient spare parts management can minimise downtime and improve overall equipment performance.
By tracking KPI for spare parts within maintenance over time, organisations can identify trends and areas for improvement in their spare parts management practices. This will help them optimise inventory levels, reduce lead times, and improve forecasting accuracy, ultimately leading to reduced downtime and improved equipment performance.
STOCKROOM VALUE COMPARED TO OVERALL INSURANCE VALUE
Correct parts at stock
Stockroom Value Compared to Overall Insurance Value is a measure of the value of the spare parts that are kept in the stockroom compared to the overall insurance value of the equipment. It is an important metric for organisations to ensure that they have the right spare parts on hand to maintain and repair their equipment effectively.
By comparing the stockroom value to the overall insurance value, organisations can determine if they are over- or under-stocking their spare parts. Over-stocking can result in unnecessary costs, while under-stocking can lead to equipment downtime.
TOP 5 USED SPARE PARTS
Most used spare parts
Top 5 spare parts “Top 5 spare parts are important to track for a number of reasons. One of the most obvious ones is the price for the spare part and how the costs add up with every replacement but that’s not all of it!
When you see that a certain spare part on a certain machine is replace rather frequently, this gives you a good hint towards the reliability of that machine. Every time a spare part is replaced, the production on that machine has to stop adding to the downtime cost of your production. In addition, the replacement and repair, demands one of the most valuable resources from you maintenance department: Time!
Use the data from your top 5 spare parts to evaluate if these can be replaced with more durable parts or if other preventive or improvement-related measures can be taken to reduce their turnover.
factor in not only the cost of the spare part but also the time that it takes your team to replace them as well as downtime costs.
TOP 5 NOT USED SPARE PARTS - SHELFWARMERS
Least (seldom) used spare parts
Top 5 not used spare parts. Here is a quick way to save money in your stockroom: Track the least used spare parts and get rid of them.Often when replacing machinery and equipment, the corresponding spare parts are not removed from the stockroom. So you might actually have spares in stock that don’t fit to any of the machines that you are currently using.There is an obvious reason why having a lot of spare parts in stock cost you money. That is the cost for storage space.
But slimming down your stockroom has more benefits to it.
-Inventory time will be reduced with a lower amount of different items
-People will spend less time searching for parts that they need as they have less stuff to go through
-Even your maintenance and stockroom system (I certainly hope it’s MaintMaster) will become faster to navigate.
There is one exception to this where you need to be careful. Some spare parts, even though you may almost never use them, are necessary to keep in stock as they may have very long delivery times, are hard or impossible to come by and their absence may cause the production to halt. We call these spare parts “insurance spare parts” and even though you need them very seldomly, you should definitely keep them in your shelf.
EMERGENCY ORDERS
Spare parts ordered in emergency
Emergency Orders refer to the spare parts that are ordered on an emergency basis in response to a maintenance or repair issue. These orders are typically placed when an organisation does not have the necessary spare parts on hand to address the issue, and the equipment is needed for production or other critical functions.
Tracking the number of emergency orders placed can be a useful KPI for organisations to monitor their spare parts management practices. A high number of emergency orders may indicate that the organisation is not adequately forecasting its spare parts needs or managing its inventory effectively. This can lead to increased costs and equipment downtime.
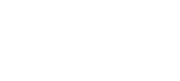
KPI Manual
Improve your maintenance strategy by using Key Performance Indicators (KPIs) to track and optimise your operations.
Download our comprehensive manual to get started.

Download our KPI Manual
Take the first step towards better maintenance with our comprehensive manual. Click to download and optimise your operations today!