Chapter 1
Maintmaster KPI Manual Why & When
KPIs as a basis for managerial decision making are becoming increasingly important. This also counts for the maintenance departments of many of our customers.
When it comes to maintenance however standardised KPIs need to be evaluated carefully. Measuring the performance of people without careful consideration can lead to unpredicted behavior.
KPIs always assume a temporal perspective. They should never be seen as a static number but rather take into account the development over time. The term Key Performance Indicator in its parts hints towards a scaling of the observation period: Performance indicators are seen as a shorter-term perspective whereas Key Performance Indicators assume a more long-term perspective. For the sake of simplicity, we will use the term “KPI” for all calculations independent of their assumed observation period.
Each KPI can in most cases be calculated on a variety of entities such as people, objects or departments and on a variety of units such as instances, hours or costs. Provided that the data is accessible, MaintMaster can calculate the KPIs whichever way desired but it remains up to the customer to decide which mode of calculation is the most promising.
OEE AND MAINTENANCE KPIS
Don’t make maintenance responsible for OEE!
Overall equipment efficiency (OEE) is based on a variety of factors. Only parts of them are within the scope of the maintenance department. Therefore it’s not recommended for the maintenance department to take responsibility for the entirety of OEE related measures!
KPIS AND TECHNICAL AVAILABITY
Maintenance has always the objective to increase the availability of production equipment under the assumption of scarce resources such as time and money. In detail, availability consists of the reliability of objects, their maintainability as well the maintenance supportability. Maintenance KPIs are always set to indicate one or several of these components.
THE MAINTMASTER MECHANICS OF KPIS
KPIs in MaintMaster are always tracked for entities such as people or objects and based on units such as costs or time. MaintMaster, being the most flexible maintenance software lets you configure KPIs on the fly in unlimited variations.
This is why you, the maintenance department get to decide which KPIs are to be monitored and on what bases they are to be calculated. But we are happy to discuss this in detail and help to set it up in MaintMaster together with you.
HOW TO IMPROVE YOUR KPI:S
KPIs mean nothing when they don’t result in actions
Most KPIs have the aim to help prioritise tasks. They may help identify the most resource-consuming objects but if there is no ambition to consequently conduct root-cause analysis or to spend time on improvement maintenance, tracking these KPIs won’t do any good. If you’re unsure where to start, a rule of thumb may be to improve one thing every day. This means working on one task a day that is marked as “Improvement Maintenance” and has the aim to increase reliability, maintainability, or supportability of a site-object.
KPI IN MAINTMASTER
Each of the mentioned KPIs can be calculated in a variety of ways. They may consider different entities such as spare parts, site-objects, people or departments. On the other hand, they can be calculated based on different units such as number of jobs, time or money.
MaintMaster is the most flexible Maintenance Software on the market. It allows you to set up all mentioned KPIs in all their variety on the fly. Even historically! – Provided that all the needed data is present.
When you run MaintMaster the first time, there are some KPIs preconfigured for you. Apart from these, MaintMaster does not give you any recommendation on which KPIs are to be tracked in what way.
This is why you, the maintenance department get to decide which KPIs are to be monitored and on what bases they are to be calculated. But we are happy to discuss this in detail and help to set it up in MaintMaster together with you.
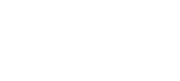
KPI Manual
Improve your maintenance strategy by using Key Performance Indicators (KPIs) to track and optimise your operations. Download our comprehensive manual to get started.

Download our KPI Manual
Take the first step towards better maintenance with our comprehensive manual. Click to download and optimise your operations today!