Chapter 5
KPI for root cause analysis
Root cause analysis KPI is a measure of the effectiveness of root cause analysis in identifying and addressing the underlying causes of equipment failures and other maintenance issues. Root cause analysis is a systematic process of identifying the root cause(s) of a problem or issue to prevent it from happening again. It involves gathering and analysing data, identifying patterns and trends, and implementing corrective actions to address the root causes of the problem.
By tracking and analysing root cause analysis KPIs, organisations can identify trends and areas for improvement in their maintenance practices and equipment reliability. This can help them optimise maintenance resources, reduce downtime, and improve overall equipment performance.
COMPLETION CODE DISTRIBUTION FOR PREVENTIVE MAINTENANCE
Chart with number of jobs / time / costs grouped by completion code and completion code group
Completion Code Distribution for Preventive Maintenance is a chart that displays the number of preventive maintenance jobs, time, and costs grouped by completion code and completion code group. Completion codes are used to classify the results of preventive maintenance activities.
The Completion Code Distribution for Preventive Maintenance chart provides valuable insights into the effectiveness of preventive maintenance activities. By tracking the number of jobs, time, and costs for each completion code and completion code group, organisations can identify trends and areas for improvement in their preventive maintenance practices.
COMPLETION CODE DISTRIBUTION FOR CORRECTIVE MAINTENANCE
Chart with number of jobs / time / costs grouped by completion code and completion code group
Root cause analysis “Completion code distribution for corrective maintenance helps to group the root cause of corrective maintenance tasks.
Examples of completion codes are handling, insufficient maintenance, wear-out failure and others
One of the most complicated completion code is handling. It indicates, that someone operating the machine slipped up resulting in a failure.
Often, maintenance technicians don’t want to point their finger at an operator but rather use another completion code to mask the real cause of the breakdown.
Therefore, the culture of the company has to allow for mistakes and errors and always seek to encourage people to learn from their mistakes rather than feel guilty and take the blame.
I have never seen an operator that breaks a machine for fun or just because they want to. Therefore, we can assume they actually want to work in the right way.
Sometimes, the root cause analysis is not only limited to finding a technical problem with a machine but also finding out what caused people to mishandling a machine.
Fixing this doesn’t require huge investments – it’s about spreading knowledge, maintaining documents and educating each other but most importantly: being open and not blame each other when mistakes are made!”
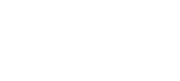
KPI Manual
Improve your maintenance strategy by using Key Performance Indicators (KPIs) to track and optimise your operations.
Download our comprehensive manual to get started.

Download our KPI Manual
Take the first step towards better maintenance with our comprehensive manual. Click to download and optimise your operations today!